Prep Stations
Complete Efficiency
Like all Nova Verta heated spray booth systems, CTOFs and Limited Finishing Workstations use three distinct operating modes to maximize the energy efficiency of the complete painting process. Nova Verta is one of the first and few that have a listing allowing recirculation of the makeup air system during preparation and cure cycles (re-circulation with direct fired heaters is not permitted per ANSI Standards or ETL on open type models). This allows for a substantial amount of fuel and electrical savings since many of these systems are typically operated in re-circulation 60 to 75% of the time. The only time the system is required to be in full exhaust mode is during paint application. Re-circulation can save thousands of dollars and should carefully be evaluated before purchasing. Another advantage afforded by re-circulation is faster drying times.
Construction
With vinyl-coated, galvanized, dual panel construction, two inches of insulation, tubular steel center, door hardware, sealing material, and nut and bolt assembly, Nova Verta prep stations, CTOF’s and double booths are built to last.
Pre-Wired
Factory pre-wiring expedites the installation of Nova’s prep stations, CTOF’s and paint booth systems. Color-coded and labeled wiring in Seal Tite conduit, and easy-to-read installation manuals minimize the need for electrical contractors and reduce setup time and expense. Finger-safe control panel wiring ensures operator safety.
Lighting
Using Class I, Division II inside access fixtures with 4 or 6 tubes each (depending on model) there is a visible difference in the technicians’ environment. Optional fixtures can be added if desired. Whatever the booth size, all strategically placed fixtures use a uniquely designed ballast and color corrective tubes to eliminate shadowing and interference with light output.
Optional is our new Industrial LED with 100,000 hour service rating Class 1 Division II
Controller
Nova Verta prep stations use Rockwell Automation-Allen Bradley components, including variable frequency drives (VFDs) and Class I, Division II touch screens to provide user-friendly long term performance and energy efficiency. Depending on model configuration, automatic or manually controlled VFDs provide optimum airflow for the refinish capabilities. VFD’s eliminate the need to adjust outdated and expensive to maintain pressure control dampers as filters gather particulates, continually altering airflow characteristics. This feature also helps to eliminate over pressurization causing unwanted turbulence during spray applications. All our panels are UL508 A. Our color Touch Screen makes Nova Verta Prep Stations and CTOF’s easy to use. Nova Verta’s operational software, which has been refined to perfection through its use on all models since 1998, includes self-diagnostics, alarm history, maintenance reminders, and logging capabilities. This advanced technology eliminates the need to send operators to extensive training programs for operation and preventive maintenance. The self-diagnostic software and non-automated technical phone support helps an operator resolve any problem in minutes rather than hours or even days.
CTOF Spray Booths
Like most Nova Verta products, CTOF Spray Booths are ETL Listed to meet stringent code requirements for unlimited painting application and provide 90% re-circulated curing capability. (Note: ANSI standards do not permit recirculated air curing or heating in direct-fired CTOF applications.) ETL Listing certifies to local authorities and consumers that our products have been scrutinized for operator and building safety and ensures they meet or exceed the national and local code requirements. Direct Fire models are optional.
CONTACT our development team to learn more about our CTOF Spray Booths.

Mix Rooms
Nova Verta Mix Rooms are available in sizes up to 150 square feet and are completely ETL Listed to meet NFPA and IFC. Constructed with the same design as our spray booths, each unit includes a four-inch spill containment. The stainless-steel mixing bench goes beyond providing required protection. It pulls hazardous vapors from the floor and protects technicians by removing hazardous vapors directly from the area where materials are mixed.
The exhausting system includes a direct drive turbine fan to move 1250 CFM, while requiring minimal maintenance. Class I Division II lights are integral to the ceiling panels and feature inside access and color corrective lighting. The Mix Room access door features auto door closer and the same quality door hardware and sealing as Nova Verta Paint Booths. For custom applications, tailor your Mix Room with features such as optional doors, a control panel, vestibules, and fascia.
CONTACT our development team to learn more about our Mix Rooms.
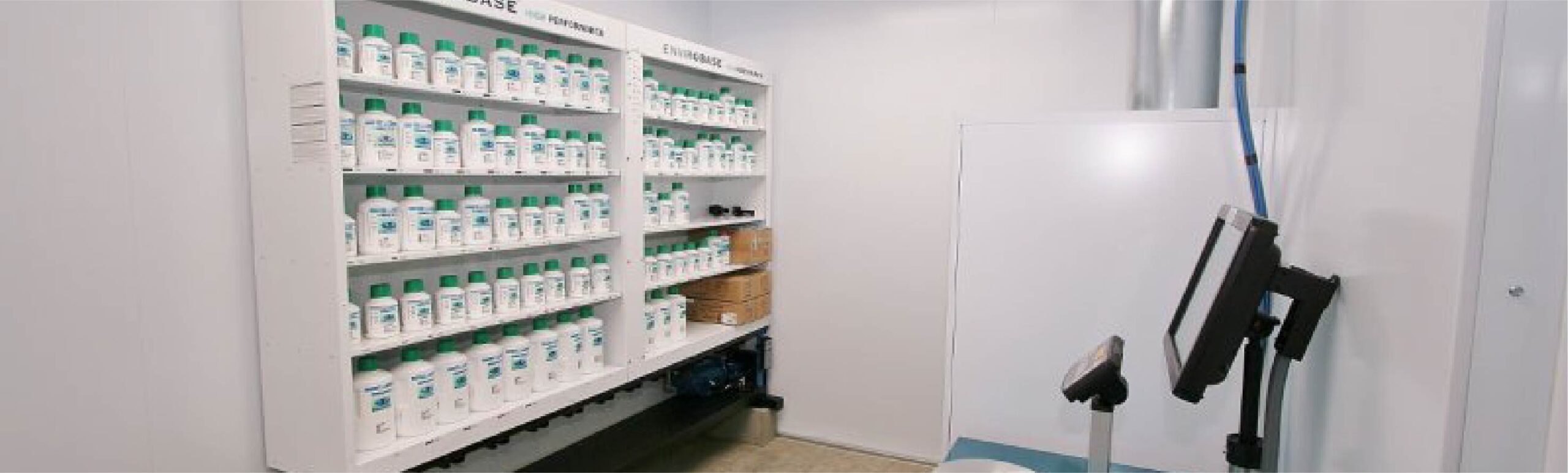
Work Stations
For smaller spray applications, get Nova Verta’s Limited Finishing Workstations. These workstations are tailored with airflow and heating capacity requirements for spray applications up to 9 square feet, which can be a concern with ever-changing paint materials. Limited Finishing Workstations offer all the same energy-efficient benefits as the CTOF models with respect to re-circulation.
CONTACT our development team to learn more about our Work Stations.

Sanding Stations
Create a safe, comfortable workplace by removing airborne particulate with sanding stations from Nova Verta. These stations are designed to move the desired amount of air and filter it prior to exhausting. Units can also be designed to re-circulate exhaust-filtered air or engineered with a damper system that allows you to choose between filtering or re-circulating air. Like the CTOF and Limited Finishing Workstations, airflow designs can be tailored to suit your needs or requirements.
CONTACT our development team to learn more about our Sanding Stations.
How much can you expect to save over the life of your booth?
Contact our development team and we'll do a custom analysis.

8207 E Trent Ave
Spokane Valley, WA 99212